EVER SO SLOWLY…
It’s been very cold, a busy time at work and with Christmas & family, plus an ongoing house project... Accordingly, my never-ending Summit project has literally been gathering dust. I have, however, worked behind the scenes with my sand blaster friend and took advantage of a recent break from ice age conditions to at least get my dream grill a little closer to reality.
Here are the cast aluminum pieces back from the sand blaster. I had tried to go it alone and just wire brush them, but the outside texture was blotchy. I didn’t want to go to a shiny smooth finish, and my efforts to camouflage the chipped off parts were a flop. Sand blasting leaves a texture more like the original finish:
I am using the higher gloss black for my firebox parts. I ran out of Rustoleum High Heat Ultra after just finishing the first coat, so I am letting them dry well - in the warm and dry inside - and then will put on one more light coat to be sure the black is completely covering. I wish now I had used Krylon’s “Max” gloss high heat, which I personally like better. The Rustoleum is fine, however.
I decided to go stock on the bolts that hold the end caps to the hood and also are used on one hole in the upper firebox. These are the visible connectors, and although I admire the quality, rugged-build look of replacing these with stainless, I opted for the blend-in black.
First I had to clean them up. Sam’s Members Mark grill cleaner did a great soak and clean:
I stuck them in an old piece of thin cardboard to paint:
Meanwhile, I also cleaned up the brackets that hold the clips for the flavorizer bars. One was bent, but my cheap Harbor Freight vice was adequate to fix that:
I did some more cleaning of the porcelain hood. It’s far from perfect with scratches and a bit of the Weber fade. At its 25th year, I accept that I can’t expect perfect. Rubbing compound DOES help get things cleaner, but it won’t remove scratches, fade, or some burned-on stuff that I had already given up on since it will be concealed:
Halfway:
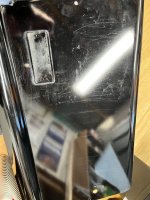
Done as I am going to get:
Lastly, I got the logo badge ready using the method proven by many here of sanding with progressively finer grade paper:
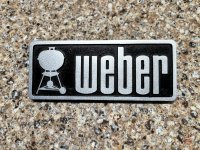
And, one non-stock mod - the classic red kettle:
I have never tried the follow up with high heat clear coat. I am thinking about it this time. Any opinions from your experience?
If the weather holds out and time allows, I hope to FINISH with painting very soon. That would leave mostly assembling the firebox with zillions of 316 stainless bolts and high heat RTV. The firebox side pieces actually have channels cast in to pour in the RTV.
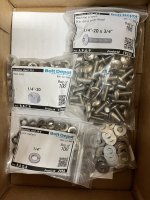
This is work that I can do inside regardless of weather. I do have burners to clean and some other stuff, but this is definitely a one slow step at a time thing

!