RalphTrimble
TVWBB Diamond Member
With the development of the RDTC amp board a new wiring scheme has become available, having the external TC amp running from the servo +5v power rather than running a dedicated 3.3v line just for the TC amp. This allows wiring the external TC Pit Probe and TWO food probes in addition to running the servo and blower over the CAT5 cable.
Here is the new CAT5 wiring chart, you must manually run jumper wires on your HM board for all items in RED:
If you look at the CAT5 jack (from Home Depot) in the following picture, you will see numbers below each wire slot and what wire colors you should use when wiring the grill end CAT5 jack manually. (I always use the set of colors closest to the wires) Note the numbers are NOT 1,2,3,4 etc... Just punch down the wires following the numbers in the above chart based on your configuration....
Here is the new CAT5 wiring chart, you must manually run jumper wires on your HM board for all items in RED:
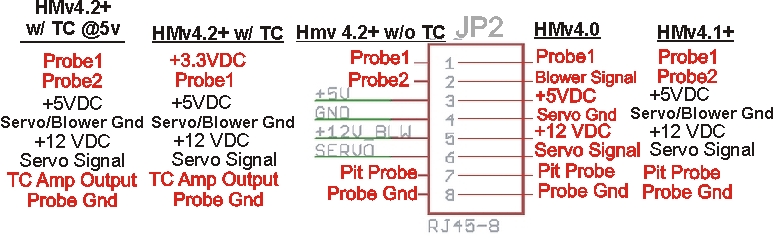
If you look at the CAT5 jack (from Home Depot) in the following picture, you will see numbers below each wire slot and what wire colors you should use when wiring the grill end CAT5 jack manually. (I always use the set of colors closest to the wires) Note the numbers are NOT 1,2,3,4 etc... Just punch down the wires following the numbers in the above chart based on your configuration....
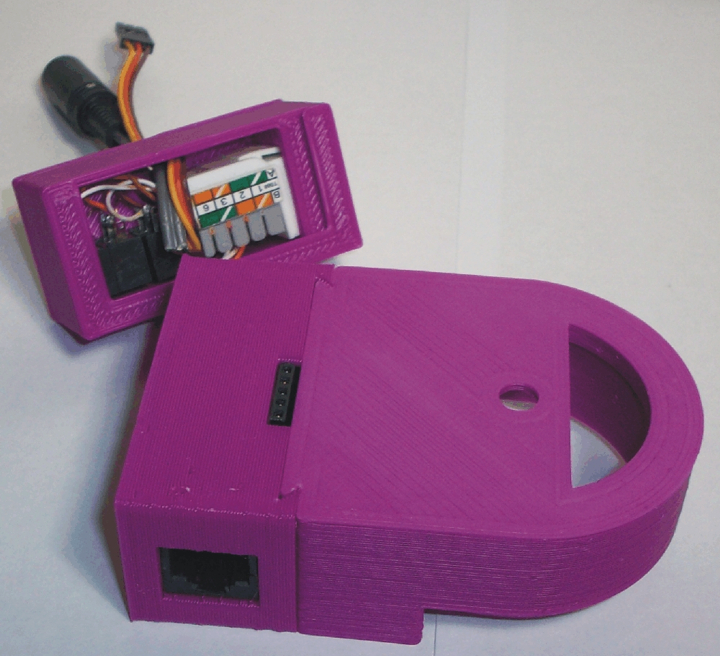
Last edited: