Hello folks! Been a while since I fixed up a grill but had a few questions since it’s been a while!
First question is likely an easy one for the veterans: how do I get the side table extensions off the Silver B? The rods seem to be nested inside side poles? Also, the plastic piece in this picture is also proving challenging to remove. Any advice?
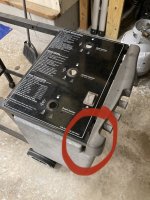
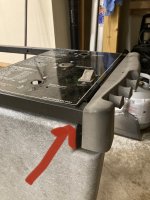
The second question: in removing the lid one hinge bolt came off easily! The other is seemingly rusted solid. I ended up simply cutting the head off it with a grinder to get the top off and not hold up the evening, but anyone have any insight into these stubborn ones?
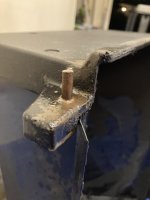
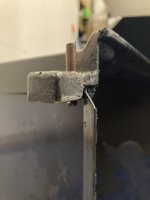
Thanks in advance! Hope all is well!
First question is likely an easy one for the veterans: how do I get the side table extensions off the Silver B? The rods seem to be nested inside side poles? Also, the plastic piece in this picture is also proving challenging to remove. Any advice?
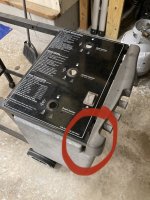
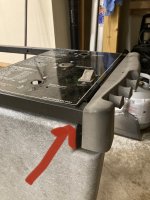
The second question: in removing the lid one hinge bolt came off easily! The other is seemingly rusted solid. I ended up simply cutting the head off it with a grinder to get the top off and not hold up the evening, but anyone have any insight into these stubborn ones?
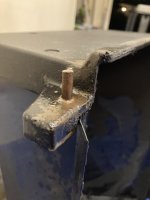
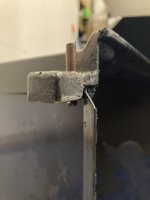
Thanks in advance! Hope all is well!