RalphTrimble
TVWBB Diamond Member
Unfortunately the temp outside dropped to about 55F last night (in JULY!), but at least it gave me a chance to see how the external thermocouple amp works over a range of temps. When I first connected the external thermocouple amp it was about 85F outside and the thermocouple tracked right with the thermistor probe, last night it tracked just as well in 55F, so that's a 30F swing and the thermocouple remained right on target. This is good news, because when I was sending the raw thermocouple output down the CAT5 cable to the amp inside the HM (inside the house) the thermocouple required a fairly large offset to read the correct temp, though once the offset was calibrated it did read perfectly. However, when the outdoor temp changes the required offset changes with it, so you would have to set your offset according to the ambient temperature, or more accurately, to the difference between the outdoor temp and the temp inside the HM unit.
I'm very happy to see the thermocouple reading the correct temp now that the amp is outside near the thermocouple junction, although 30F is a fair swing in temps it's nothing compared to the winter temps we see here in the midwest, thankfully I will have to wait at least a few months to test it in those sub freezing temperatures....
Edit:
Here is a screen shot of the thermocouple with the external amp and a ThermoWorks Pro thermistor probe from the cool evening last night through the warm day today. They track very close, though the thermocouple has a quicker response so you see it react a bit more to temperature changes caused by sunshine/clouds etc when the fire isn't burning. I still have yet to see the noise indicator pop up even while sending the probes over the very long CAT5 cable, which is of coarse good news, I guess those RC filters are really doing their job!
I'm very happy to see the thermocouple reading the correct temp now that the amp is outside near the thermocouple junction, although 30F is a fair swing in temps it's nothing compared to the winter temps we see here in the midwest, thankfully I will have to wait at least a few months to test it in those sub freezing temperatures....
Edit:
Here is a screen shot of the thermocouple with the external amp and a ThermoWorks Pro thermistor probe from the cool evening last night through the warm day today. They track very close, though the thermocouple has a quicker response so you see it react a bit more to temperature changes caused by sunshine/clouds etc when the fire isn't burning. I still have yet to see the noise indicator pop up even while sending the probes over the very long CAT5 cable, which is of coarse good news, I guess those RC filters are really doing their job!
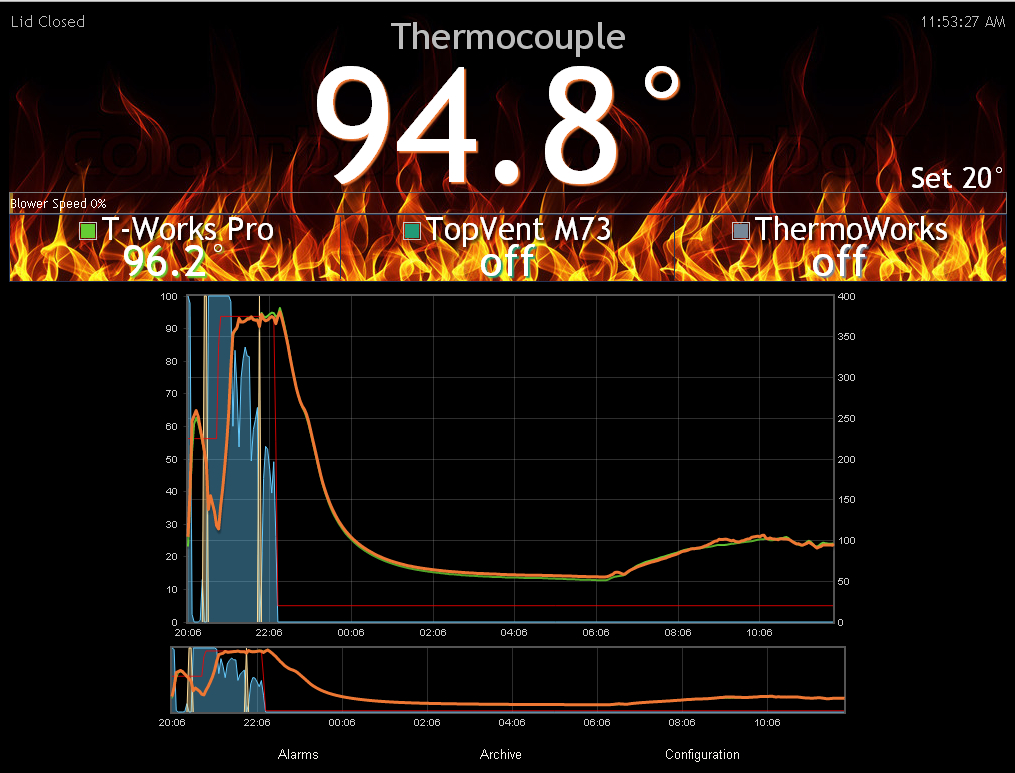
Last edited: