One of my most favorite things about the heatermeter is being inspired by others work to make something better. A long time ago someone had an "air burner" system made of copper pipe underneath the charcoal grate. I thought it would be cool to not have to deal with the ash falling down around the bottom and came up with this..
The Ring of Fire.
A few brass fittings, some copper fittings, and some soft copper. Full material list down below.
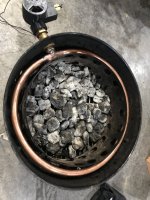
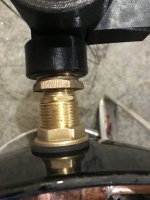
FYI - I'm using the adaptadamper with aux board which has a 1" FNPT outlet. Starting at the fan here is the material list.
1" x 3/4" brass reducing bushing
3/4" MNPT x 3/4" GHT adapter
3/4" GHT x 1" brass bulkhead with rubber grommets
3/4" wrot copper FTG x male adapter
3/4" wrot copper tee
3/4" soft copper tubing (~5' length, longer if needing to bend it)
I'll try and share some links for above when not on the phone.
Only special instructions are the bulk head has 3/4" GHT internal threads. I had originally bought some npt to ght adapters to transition inside the wsm. However, due to limited room between the outside of the lower bowl and the charcoal ring I had to come up with an alternative. The branch of the 3/4" tee I reamed down to a shorter neck with a step bit. Then did the same for the 3/4" male adapter. The depth of the tee ended up about 1/4" or so. Then in order to get the shortened 3/4" male adapter into the 3/4" GHT bulkhead I used a 3/4" NC die to remove the tapered npt threads and straight cut them. Not ideal, but we're just blowing air on a fire right?
There are 12 evenly spaced out holes, approximately 3/32" diameter. Each hole is drilled slightly down from level to direct air to the charcoal ring. I may look at enlarging these, obviously had to raise my max fan speed up from my previous setup (think side mount dog bowlish style) but was able to back down into 70-80% max fan speed during my trial run with an 8lb pork butt and still maintain temps even at the end of the cook.
The Ring of Fire.
A few brass fittings, some copper fittings, and some soft copper. Full material list down below.
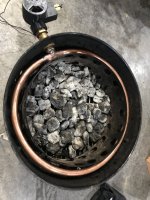
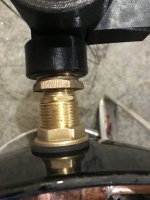
FYI - I'm using the adaptadamper with aux board which has a 1" FNPT outlet. Starting at the fan here is the material list.
1" x 3/4" brass reducing bushing
3/4" MNPT x 3/4" GHT adapter
3/4" GHT x 1" brass bulkhead with rubber grommets
3/4" wrot copper FTG x male adapter
3/4" wrot copper tee
3/4" soft copper tubing (~5' length, longer if needing to bend it)
I'll try and share some links for above when not on the phone.
Only special instructions are the bulk head has 3/4" GHT internal threads. I had originally bought some npt to ght adapters to transition inside the wsm. However, due to limited room between the outside of the lower bowl and the charcoal ring I had to come up with an alternative. The branch of the 3/4" tee I reamed down to a shorter neck with a step bit. Then did the same for the 3/4" male adapter. The depth of the tee ended up about 1/4" or so. Then in order to get the shortened 3/4" male adapter into the 3/4" GHT bulkhead I used a 3/4" NC die to remove the tapered npt threads and straight cut them. Not ideal, but we're just blowing air on a fire right?
There are 12 evenly spaced out holes, approximately 3/32" diameter. Each hole is drilled slightly down from level to direct air to the charcoal ring. I may look at enlarging these, obviously had to raise my max fan speed up from my previous setup (think side mount dog bowlish style) but was able to back down into 70-80% max fan speed during my trial run with an 8lb pork butt and still maintain temps even at the end of the cook.